Metallisation


The manifolds shown have been pre-treated with our plasma coat system and a further ceramic coat applied.
The advantages are as follows:
1. Full two-year rework guarantee.*
2. Helps reduce further heat loss above 200c
3. Preserves & protects cast iron & mild steel items & extends serviceable life. Also can be applied to stainless steel.
4. Prevents corrosion.
5. Helps to fill corrosion pitting.
6. Will not crack or flake.
7. Can be coated in any suitable high-heat coating.
8. Offers heat reduction by up to 35% when both coats have been applied.
* Subject to the condition.
Will have a matte appearance with a slight texture finish.
See the following page for further details https://ctc- powder-coating.co.uk/plasma- coating/
Basecoat protection applied. Pure zinc metallization coating.
Wood table top zinc metalization coat, linished & clear lacquer coat
Alloy Coated Exhausts

Landrover bulkhead


Callipers
These callipers were badly pitted by corrosion and required extra time and attention. After a careful blast clean a layer of pure aluminium ark spray applied (metallization) to repair the damage this was cut back leaving a smooth surface and the final ceramic finish not only looks good it will provide long term protection. Metallization info can be found on our website.



Metallisation, first video shows the application of pure zinc base coat, second video shows applying pure copper coat, this finish can be part polished or antique fluids applied to give that weathered look. In the second video also you will see a hardwood sample being coated with a copper finish and again can be sanded or polished highlighting the raised wood grain. Zinc prime coat serves as a very effective anti corrosion coat that can be used on many items inducing car chassis, body panels, bike frames etc and is happy with any type of wet primer paints. With the added bonus of filling in rust pin holes after blast cleaning. In fact (zinc) as we have carried out some test samples can be applied to cardboard, resin base materials for instance for film studious scenery. The Star gate(tm) was zinc coated (not by us) but shows how effective this product is.

Maldon Shot Blasting & Powder coating Ltd is now offering -: Thermal or metal spraying steel to protect it from corrosion has always been recognised as a long-term solution for many industries and has many advantages over hot dip galvanising.
• Low heat input during spraying eliminates the risk of thermal distortion
• Low heat input eliminates the risk of thermal metallurgical degradation
• Sealed hollow fabrications may be treated without risk of explosion
• The process is not limited to zinc. The coating material may be selected specifically for the environment.
• Coating thickness may be varied from place to place to provide extra protection in critical areas
• There is no limit to the size of article which can be treated
• Articles can be treated on site
• There is no effluent disposal problem
• Reduced stocks of zinc are required. Working capital is not tied up in a molten zinc bath
• Fuel is not needed to keep zinc molten when the process is not working
• Metal spraying is used to restore corrosion protection on damaged areas of welded galvanised
steel.
Anti Corrosive Finishing
Metal or thermal spraying is a technology, which protects and greatly extends the life of a wide variety of products in the most hostile environments and in situations where coatings are vital for longevity. The variety of metallised coatings is vast but can be broken down into two main categories. These include finishing coatings, such as anti-corrosion or decorative coatings, and engineering coatings such as wear resistant and thermal barrier coatings.
Metal spraying is carried out in a wide range of anti corrosion and engineering markets, including oil and gas, construction, petrochemical and marine. Corrosion is a major problem for these industries. There are four commonly used processes in thermal spraying; Flamespray, Arcspray, Plasma Spray and High Velocity Oxygen Fuel (HVOF), but only two of these, Flamespray and Arcspray are normally used for finishing coatings.
DOWNLOAD PDF >> Metallisation
COMPARISON OF METAL
SPRAYING WITH
GALVANISING
Technical Bulletin 5.7.9.2
Galvanising is a well established process for applying a corrosion protection layer of zinc to steel.
Treated steelwork is immersed briefly in molten zinc and the coating builds up very quickly.
Galvanised layers are usually of even thickness, dense and metallurgically bonded to the steel.
Thickness is typically 0.002 – 0.006 in (50 – 150μ). Coating compositions are sometimes varied to control deposit thickness and give better protection in certain specific environments.
Metal Spraying Offers the Following Advantages Over Galvanising
• Low heat input during spraying eliminates the risk of thermal distortion
• Low heat input eliminates the risk of thermal metallurgical degradation
• Sealed hollow fabrications may be treated without risk of explosion
• The process is not limited to zinc. The coating material may be selected specifically for the
environment
• Coating thickness may be varied from place to place to provide extra protection in critical areas
• There is no limit to the size of article which can be treated
• Articles can be treated on site
• There is no effluent disposal problem
• Reduced stocks of zinc are required. Working capital is not tied up in a molten zinc bath
• Fuel is not needed to keep zinc molten when the process is not working
• Metal spraying is used to restore corrosion protection on damaged areas of welded galvanised
DOWNLOAD PDF >> Comparison
Thermal Spraying Stands the Test of Time
Thermal or metal spraying steel to protect it from corrosion has always been recognised as a long-term solution for many industries. UK based Metallisation has been providing anti corrosion solutions for over 80 years, to a diverse range of industries all around the world. One of its successes is the anti corrosion protection of bridges, including the Forth Road Bridge. DOWNLOAD PDF >>Thermal Spraying
Metallisation
Application Data Sheets DOWNLOAD PDF >> Metallisation-DATA_SHEETS
See info on Petrol Tank Metallisation Repair…

Post by Maldon Shot Blasting & Powder Coating Ltd Heybridge Essex CM9 4ER
Repaired Manifold – Using Metallisation
Repair of manifold. Blast cleaned and 2 coats of Zinc metallisation applied, Giving a new lease of life, this system is extremely effective for long term protection, keeps the heat loss down by at least 20% and also very good for filling small blow holes without the need to weld. Heat paint can be applied to the zinc surface. Furthermore this is an inexpensive solution over other systems.
This VW body pan had the full anti-corrosive treatment.
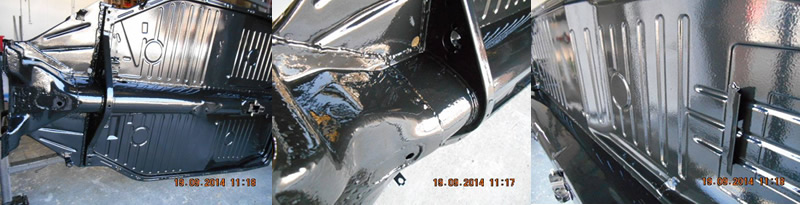
Schedule of work:
Clean and remove dirt & grease contaminants, blast clean leaving a clean etched & rust free surface.
Apply 100 micron coat of 99.9% pure zinc metallization coating all areas and masking off all threads. Degas to remove any trapped gas built up within the zinc coat.
Remove from the curing oven and apply the first coat of Gloss black Plascoat PPA-571 (no primer coat required) whilst the material is still hot, this helps adhesion to the more difficult parts to reach .Bake off and reapply second hot coat. The overall final coats will be around 300 microns inc zinc coat. The added weight to this will be around 8 kgs.
https://ctc-powder-coating.co.uk/our-work/plascoat/
This system not only gives a high gloss or semigloss finish it also offers extreme long term anti corrosion properties. There are other colours in the range to choose from. Yellow, Blue, Light or dark grey, brown, black, red, green & white.
The overall cost on this project came to £450.00 plus vat. Making the work cost effective and reliable in the long term over the traditional work.
Further information.
The metallization system can be used on most car body parts, motorcycle frames and products used in extreme conditions. . Aluminium panels are not suitable for zinc metallization due to the re-action between the two materials, however a pure aluminium material is used that also offers very good long term protection. Also on offer is. Copper, brass, babbitt and many more materials including pure silver & gold.
Another point to note is for zinc or Aluminium spray can also be used to fill small corrosion damage and pin holes, thus saving time and effort using standard unreliable body fillers. Please note this will not give any structural strength.
For inner surfaces that can not be treated or reached as box rails we can apply a heavy coat of Wax oil to finish the job if required.
So if you are serious and want the best possible long term solution that any car restoration company would be very hard pushed to match then the above system is the one to choose.
MSB would be happy to work alongside any restoration company to advise and offer this service.
Please feel free to contact our office on 01621 841100.
Plascoat offers.
Superior resistance to sun, salt and sea water
Excellent impact and sand abrasion resistance
Premium quality, glossy appearance
Will not crack, chip, flake or fracture
Low temperature performance to -70°C
Excellent adhesion to steel, iron and aluminium
No requirement for a primer
Metallisation complete with a new lease of life…
Petrol Tank Metallisation repair
I had my doubts that this would work but to me surprise it done the business.
No need for cutting and welding this was completed by pure zinc metallisation
Metallisation Bird Bath
Metallisation. 99.9% pure copper coated cast concrete bird bath. Given a few months of natural weathering it will look like an antique garden ornament. This can be carried out on just about any material including hard wood, plant pots, steel, cast iron.
Exhaust system blasted & zinc metallised
Metallisation. Giving a much extended life over standard pressed steel..
Blast clean & zinc metallisation
A somewhat unusual approach but this is what the client requested. Blast clean & zinc metallisation. We asked if he was sure. We prefer the parts to be removed before we start on such work.
We accept all major credit and debit cards
Copyright © 2020 CTC Powder Coating. All Right Reserved.
Designed by Applied Image Limited
2018 © CTC Powder Coating
You can also find us on:
https://www.performance-coatings.co.uk/
http://www.powdercoated-customcarparts.co.uk/